Many warehouses rely on qualified stretch wrap machine repair to keep their systems running.
Many warehouses rely on qualified stretch wrap machine repair to keep their systems running.
Blog Article
A Comprehensive Strategy to Addressing Stretch Cover Maker Repair Service Obstacles
You understand that stretch wrap equipments are vital for preserving performance in packaging procedures. Problems can emerge that interfere with productivity. What are the best techniques to ensure your makers run efficiently?
Comprehending Common Stretch Cover Maker Issues
When you rely on stretch cover equipments for reliable product packaging, it's essential to recognize usual issues that can interrupt procedures - stretch wrap machine repair. One prevalent problem is irregular stress, which can cause insufficient wrapping and compromised load stability. If you see the movie isn't sticking effectively, check for worn-out rollers or improper setups
Another problem you could encounter is movie damage, usually brought on by incorrect movie kind or machine breakdowns. Regularly check the equipment for indications of wear and tear to avoid this.
Additionally, keep an eye on movie build-up or jams, which can halt manufacturing. Usually, this takes place because of misalignment or particles in the machine.
Finally, inappropriate sealing can result in loads coming apart throughout transportation. Make sure your machine is calibrated appropriately to maintain the honesty of your plans. By remaining cautious and dealing with these concerns promptly, you can facilitate smoother operations.
The Relevance of Normal Preventative Upkeep
Routine preventive upkeep is vital for maintaining your stretch wrap machine running smoothly and efficiently. By regularly examining and servicing your tools, you can spot possible concerns before they escalate into costly repair services. This proactive approach not just prolongs the lifespan of your maker however additionally assures that it runs at peak performance.
You ought to arrange regular assessments to clean, oil, and change used parts. Maintaining your maker calibrated aids maintain perfect wrapping high quality, lowers waste, and improves performance. Furthermore, documenting upkeep activities creates a reliable history that can inform future decisions.
Don't forget the value of training your team on upkeep finest methods. When everybody understands exactly how to look after the machine, you reduce the danger of operator error leading to break downs. In other words, committing to normal preventive upkeep is a smart financial investment that pays off in reduced downtime and boosted efficiency in your procedures.
Troubleshooting Methods for Quick Services
Reliable troubleshooting methods can greatly lower downtime when your stretch wrap machine experiences issues. Is the maker not wrapping correctly or is it making uncommon noises?
Next, inspect the equipment's settings and controls; often, a basic change can resolve the problem. Check the movie tension and placement, as incorrect setup can cause wrapping failures. Don't neglect electrical connections; loosened or damaged cords can interrupt performance.
If you're still dealing with difficulties, consider running diagnostic examinations if your device has that capability. Paper each action you take, as this can assist in future troubleshooting and repair work. Do not think twice to seek advice from with a specialist if you can not fix the issue rapidly. Reliable troubleshooting keeps your procedures running smoothly and reduces expensive hold-ups.
Educating Operators for Effective Device Use
To ensure your stretch wrap device operates at peak efficiency, correct training for drivers is necessary. When drivers comprehend the device's performances, they can maximize its possible and decrease downtime.
Motivate them to practice under supervision, resolving any type of concerns or problems they may have. Frequently arranged correspondence course can maintain their abilities sharp and help them adapt to any type of updates or modifications in modern technology.
Additionally, instill a society of accountability by empowering drivers to report concerns or suggest improvements. This proactive approach not just improves their confidence but also adds to the general effectiveness of your operations. With trained operators, you'll see fewer mistakes and raised performance, ensuring your stretch cover maker stays an important possession.
Building a Solid Interaction Channel Between Teams
Well-trained drivers can just do at their finest when there's a solid interaction channel in between groups. Efficient interaction removes misunderstandings and guarantees everybody's on the same page regarding maker procedures and repair service needs. Motivate normal check-ins and meetings to go over concerns, share insights, and address issues.
Making use of innovation, like messaging apps or collaborative platforms, can boost real-time communication, making it much easier to report troubles and share updates swiftly. Designating clear duties and responsibilities promotes responsibility, permitting employee to connect to the ideal individual when issues arise.
In addition, creating an open environment where everybody feels comfy sharing responses can bring about innovative remedies. By prioritizing interaction, you're not just boosting maker performance; you're also developing a cohesive group that functions with each other flawlessly. This joint spirit inevitably leads to quicker fixings and reduced downtime, benefiting the entire procedure.
Purchasing Top Quality Substitute Components
When it involves keeping your stretch cover makers, spending in high quality replacement parts is vital for making sure trustworthy efficiency and lessening downtime. Economical alternatives may seem tempting, yet they usually bring about even more considerable concerns down the line, costing you extra out of commission and shed efficiency. By choosing high-quality components, you're not simply repairing a problem; you're improving the overall performance of your tools.
Furthermore, quality components are usually manufactured to more stringent requirements, which means they'll fit better and work more accurately. This decreases the likelihood of unanticipated break downs, allowing your procedures to run smoothly. Reputable suppliers usually supply service warranties, providing you tranquility of mind in your investment.
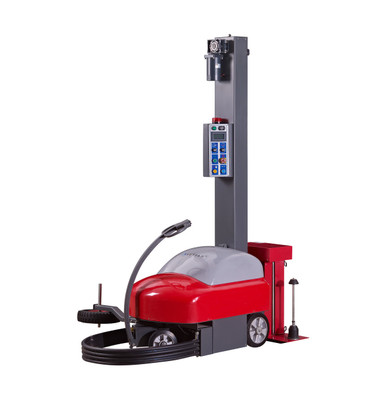
Assessing Performance Data for Continuous Improvement
To boost your stretch wrap maker's efficiency, you require efficient information collection strategies. By reviewing efficiency metrics, you can determine locations for renovation and boost efficiency. Identifying these opportunities not only streamlines procedures yet additionally lowers downtime and repair work costs.
Data Collection Methods

Efficiency Metrics Assessment
While evaluating performance metrics, it's important to focus on specific data points that straight affect your stretch wrap equipment's performance. Begin by tracking cycle times, as they disclose exactly how rapidly your maker operates under typical problems. Screen downtime incidents to recognize patterns or persisting issues that might require addressing. Keep an eye on film use, ensuring you're not wasting product, which can affect costs and efficiency. Furthermore, evaluate result top quality by looking for incongruities in the wrapping procedure. By analyzing these metrics regularly, you can pinpoint locations needing interest and take positive steps. This continuous examination helps improve productivity, decrease costs, and ultimately improve your maker's long life, resulting in a more effective wrapping operation in general.
Determining Improvement Opportunities
As you examine performance data, you can reveal beneficial improvement chances that enhance your stretch wrap maker's efficiency. Try to find patterns in downtime, cycle times, and cover quality. By recognizing patterns, you'll see which locations require attention. For instance, if constant malfunctions associate with specific operating conditions, you can change procedures to minimize these issues. In addition, contrast your data against industry criteria to gauge your efficiency. Involve your group in discussions about the findings; their insights can expose useful solutions. Carrying out small changes based on this analysis can result in substantial gains in performance. Consistently taking another look at and upgrading your efficiency information will guarantee constant renovation, keeping your operations running smoothly and effectively.
Regularly Asked Inquiries
Just How Can I Tell if My Maker Needs a Repair or Just Maintenance?
To inform if your maker needs fixing or just upkeep, pay attention for uncommon noises, look for irregular performance, and check for noticeable wear. If problems persist after upkeep, it's likely time for a fixing.

What Is the Ordinary Lifespan of a Stretch Wrap Device?
The standard life expectancy of a stretch wrap device is usually five to 10 years, depending on usage and maintenance. Regular care can extend its life, so keep an eye on performance and address concerns quickly.
Are There Specific Brands Recognized for Better Dependability?
Yes, some brands are understood for their dependability. You'll locate that business like Signode and Lantech typically obtain favorable testimonials - stretch wrap machine repair. Researching user responses can assist you pick a trustworthy stretch wrap device for your needs
What Are the Signs of Poor Driver Training?
If you discover regular mistakes, irregular covering, or safety events, those are signs of inadequate operator training. Lack of recognizing concerning maker features or failure to follow procedures can considerably affect efficiency and security.
Exactly How Can I Discover a Professional Technician for Repairs?
To locate a certified technician for repair services, ask for recommendations from my explanation industry peers, check on-line testimonials, and confirm accreditations. You might additionally consider contacting neighborhood devices suppliers who typically have actually trusted service technicians on hand.
Conclusion
To summarize, dealing with stretch cover equipment repair service difficulties needs a proactive technique. By prioritizing preventive maintenance, providing comprehensive driver training, and spending in high quality parts, you can greatly minimize downtime and enhance performance. Don't fail to remember the relevance of solid interaction in between teams and continual assessment of device output. By carrying out these techniques, you'll not only improve wrapping top quality but additionally foster a society of effectiveness and improvement in your operations. Keep in click for source advance of problems prior to they arise!
Report this page